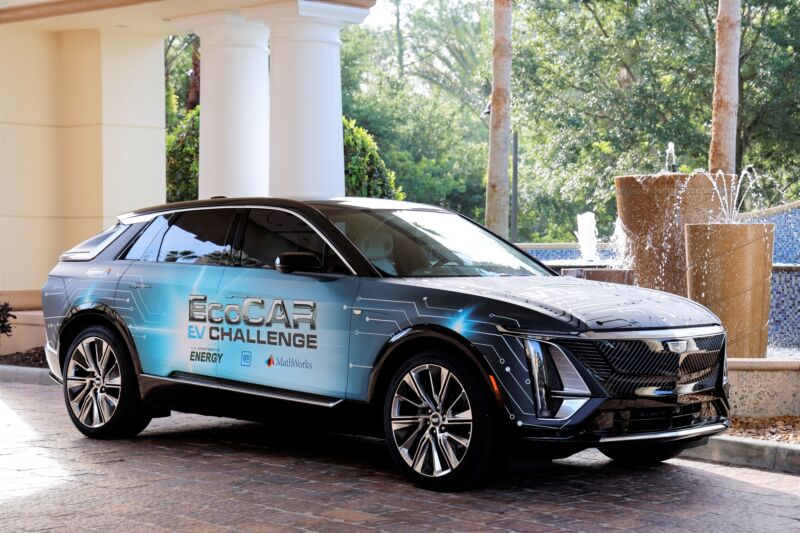
EcoCar
Across the country, teams of students at 15 different universities are in the middle of a four-year project, dissecting an electric vehicle and figuring out ways to make it even better. The program, called the EcoCar EV Challenge, was founded more than three decades ago by the US Department of Energy and is run by the DOE’s Argonne National Laboratory.
Over the last 35 years, more than 30,000 students from 95 universities have participated in the EcoCar Challenge, part of the DOE’s Advanced Vehicle Technology Competition. Each segment spans four years, with the most recent cycle beginning in 2023 with a new Cadillac Lyriq donated by the General Motors automaker.
The students take this competition very seriously, as participation alone brings a lot of benefits, including the potential for a lifelong career path.
Mobility advancement in progress
One of the organization’s goals is to challenge teams to “identify and address specific challenges with equity in the future of mobility through the application of innovative hardware and software solutions” while working with underserved populations. Through this process, the student-run teams are discovering untapped potential for future EV development and finding solutions that could help local and national communities.
The entire first year is packed with intense research and planning. Students don’t even get to put their hands on a car until year two; meanwhile, they learn how to work together and communicate as a team. They run simulations with propulsion controls and modeling, and by the time they have access to a vehicle, they’re ready to dive in.
University of Alabama student Corban Walsh explains that during the prototyping process, automakers like Cadillac end up with a fleet of pre-production vehicles that can’t be resold. Walsh and his team were given a practically new all-electric Lyriq with just 17,000 miles (27,400 km) on it, and they decided their goal was to transform it from a rear-wheel-drive to an all-wheel-drive configuration and boost the horsepower from 300 to 550 (223 to 373 kW). With tasks like that, one might think this is an ideal club for car fanatics. But Walsh says the team has diverse interests and is in fact very software- and planning-focused.
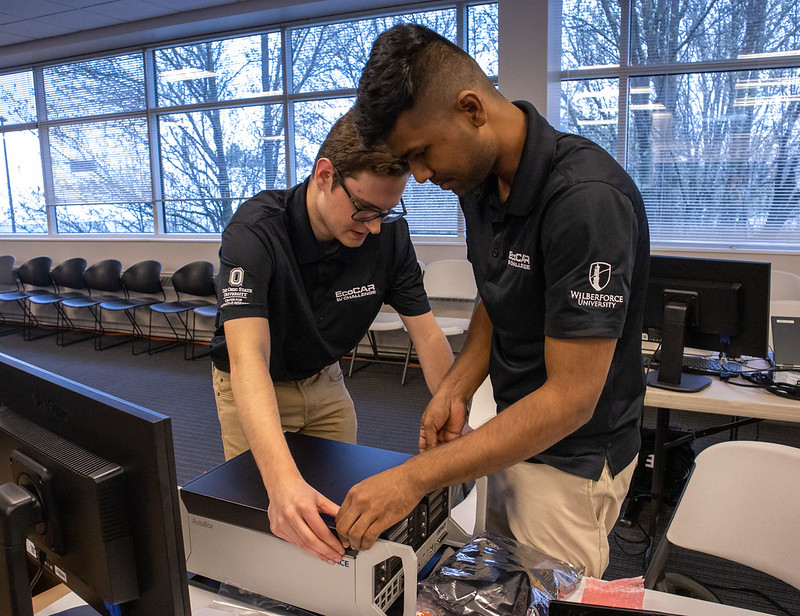
Year one is research and planning.
EcoCar
“In some ways, we attract the ‘car guy’ type of person, but at the end of the day, you don’t have to be a car guy,” Walsh says. “You can even forget it’s a car sometimes.”
Any student can join the EcoCar EV Challenge, and general onboarding familiarizes them with the tracks and teams they can join. First, they take a lab tour and view required safety videos; then, they choose a subteam under the general categories of hardware, integration, and software development. The Connected and Automated Vehicle Features subteam, for example, integrates sensor hardware and software, stitching together the data.
Along the way, small tasks lead to big advances. One of the first orders of business for the Lyriq was to obtain a clean title and registration as a salvage vehicle to be considered road-legal. Teams strip the cars down as far as they can, sometimes moving forward through a series of trials and errors. They read all the manuals they can get their hands on, consulting with their GM mentor when they get stuck.
GM also supplies some parts, allowing students to order a limited number from the catalog. The University helps defray some of the cost, and companies like American Axle donate critical components like motors. Natick, Massachusetts-based Mathworks provides the simulation software the team needs for planning. Students learn how to use the resources available on campus, too.
“One of the hardest but coolest things we’ve worked on was when we had to plan mountings for two new motors,” Walsh says. “We decided to use the on-campus foundry where we can cast these parts.”
The foundry had excellent advice for the team, Walsh says, helping them figure out how to make mountings that were strong enough to hold the motor and won’t cause corrosion. They 3D-printed the part and made a ceramic mold, then burned out the plastic and let the metal harden.
+ There are no comments
Add yours